Mastering T-Shirt Stamping: Techniques and Tips
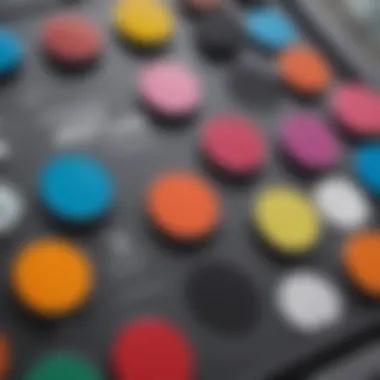
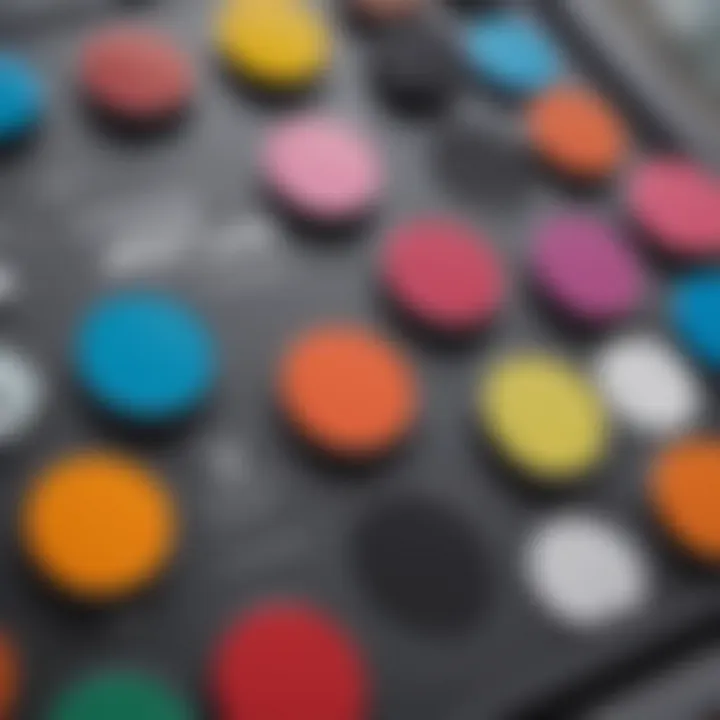
Intro
Stamping t-shirts combines creativity and technicality, allowing designers to express unique ideas while producing high-quality apparel. Whether you are a hobbyist looking to explore a new project or a seasoned professional aiming to refine your techniques, understanding the process of t-shirt stamping is essential. This introduction will provide insights into the significance of stamping in garment design and open the door to various techniques that keep evolving.
A vital aspect is the correct selection of materials. These choices not only carry directly into the quality of the final product but also affect ease of use during the stamping procedure. This guide is tailored to both beginners and those with more experience and will cover the[* essentials*] like design preparations, various stamping methods, materials, and troubleshooting common issues.
Thus, our journey into t-shirt stamping begins, examining its nuances and imparting knowledge designed to elevate the craftsmanship of t-shirt creators.
Equipment Reviews
Essential Materials
To successfully stamp t-shirts, you first need to gather the right materials. Here, we break down what’s required:
- T-shirt Fabric: Choose cotton or a cotton-blend fabric for best results. This ensures that the design adheres well and maintains durability over time.
- Inks: Water-based or plastisol inks are common for t-shirt stamping. Each type has merits; for example, water-based inks are eco-friendly while plastisol inks provide vibrant colors with an opaque finish.
- Tools: Depending on your technique, tools like screens, squeegees, and heat presses become essential components.
- Design Displays: Using software like Adobe Illustrator or Silhouette Studio will greatly enhance your design capabilities before stamping on fabric.
Techniques Overview
In t-shirt stamping, a variety of methods exist. Not all are suited for every project. Here’s a snapshot of popular techniques:
- Screen Printing: Often favored for bulk designs, this method offers precision and efficiency.
- Heat Transfer: Ideal for intricate designs, heat transfer uses thermal application to bond the design to the fabric.
- Direct to Garment (DTG): This newer method is comparable to a printer but specifically for textiles. It allows for full-color prints that look and feel good.
Investing in quality materials and choosing the right method for your anticipated outcome is crucial.
Common Challenges and Solutions
When it comes to stamping t-shirts, certain obstacles may occur. Here are a few along with their possible solutions:
- Inconsistent Prints: If your prints vary significantly from one shirt to another, check the alignment of your screens or printing heads. Review the pressure applied during printing.
- Ink Bleeding: This can occur when too much ink is applied or if the fabric is improperly prepared. Sticking to light layers and ensuring a well-prepped surface will help prevent this.
- Design Misalignment on Press: A loss of precision can emerge when setting up your prints. Use jigs and guides to improve consistency.
By being aware of these common difficulties and working to counteract them, you will establish a smoother printing environment. This leads to successfully crafted t-shirts that fulfill creative impulses.
Stay tuned! In the following sections, further insights into tools, methods, and practical tips will be shared, ensuring a broader grasp of putting your designs on fabric more effectively.
Preface to T-Shirt Stamping
Stamping t-shirts has grown in popularity as a creative and pragmatic way to express individuality. While the craft may seem straightforward, the intricacies involved make understanding the fundamentals crucial for achieving quality results. T-shirt stamping is not only a means of decorating clothing but also a form of self-expression, brand promotion, and business opportunity. Addressing these aspects aids in comprehending the wider implications of this craft.
Understanding the Basics
When talking about stamping t-shirts, it is vital to comprehend the fundamental principles. This involves familiarity with processes like ink application, pressure adjustment, and heat requirements. Each method may demand slightly different skills and judgements. Recognizing the three main types of inks—water-based, plastisol, and discharge—can determine the look and feel of the final product. Additionally, knowing which tools and platforms are involved helps novices better visualize the requirements.
Clean workspace setup and functionality are also part of the basic knowledge one must acquire when starting with t-shirt stamping. Understanding factors such as fabric choice affects both technique application and the gear required for the assignment. Whether one aims for vibrancy or durability, each choice resonates through the finished design, impacting satisfaction.
Importance of Design in Stamping
The role of design cannot be overstated in t-shirt stamping. A well-thought-out design lays the groundwork for executing the project effectively. Creative expression should resonate within the crafted design, reflecting personal or brand identity. Shades, tones, and patterns chosen influence visual impact significantly. Poor design may lead to incomplete messages, muted appearances, or an unprofessional look.
Furthermore, good design promotes coherence across multiple items if designed for promotional or merchandising purposes. A unified theme or distinctive logo can create memorable visual identity in any kitesurfing or extreme sports superbly targeting athletes's attention. Factors such as readability and placement should also be carefully considered.
Taking into account unexpected reactions to various inks and materials is another important aspect that could crop up in stamping projects. Therefore, continuously evaluating and validating designs before pressing go-live can avoid many blunders. Understanding the design principles shapes the very essence that distinguishes exceptional t-shirts from the mediocre ones, and contributes to success both for personal endeavors and in wider contexts.
Materials Needed for T-Shirt Stamping
Understanding the necessary materials for t-shirt stamping is vital for anyone looking to achieve optimal results. The right tools can make a significant difference in both the quality of the final product and the overall efficiency of the stamping process. Each component plays a unique role, and neglecting even a single element can lead to underwhelming results. In this section, we will explore the various types of inks and paints, factors to consider for selecting fabrics, and essential tools and equipment required for efficient stamping.
Types of Inks and Paints
Selecting the right ink or paint is perhaps the most crucial decision in t-shirt stamping. Inks and paints differ not just in color but in formulation and durability.
- Plastisol Ink: This type of ink is widely used among professionals due to its lasting power. It sits on top of the fabric, which enhances vibrancy but may require special curing methods.
- Water-Based Inks: As the name implies, they use water as a base, leading to less environmental impact. However, the colors may be less vibrant and require careful application and drying time.
- Discharge Inks: Suitable for darker fabrics, this ink removes the dye from the shirt fabric, leaving a print of the original color. This process can be complex but yields unique results.
- Acrylic Paint: Often more accessible for novices, this type of paint can adhere well, but may not withstand extensive washing.
Each of these inks and paints has a different application process. Consider applying a sample to see how colors interact with fabric types before beginning a full project.
Selecting the Right Fabric
The fabric you choose for stamping impacts not only how the ink adheres but also the washed clothing durability. It is important to match your designs and stamping type with appropriate material types.
- Cotton: Natural fibers like cotton are punctuated for their flat textures. They generally take ink well.
- Polyester: This synthetic fabric holds vibrant colors beautifully, making it a smart choice for sublimation techniques.
- Blends: Fabrics that combine cotton and polyester can provide a strong compromise. They may perform well in various printing methods but be sure to test the ink compatibility before proceeding.
When grading fabric for an upfront project, consider weight. Heavier fabrics may be more durable but tricky to work with for medium detail artwork.
Essential Tools and Equipment
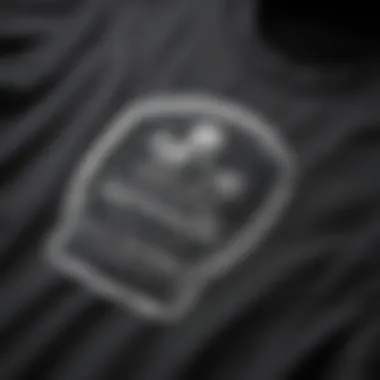
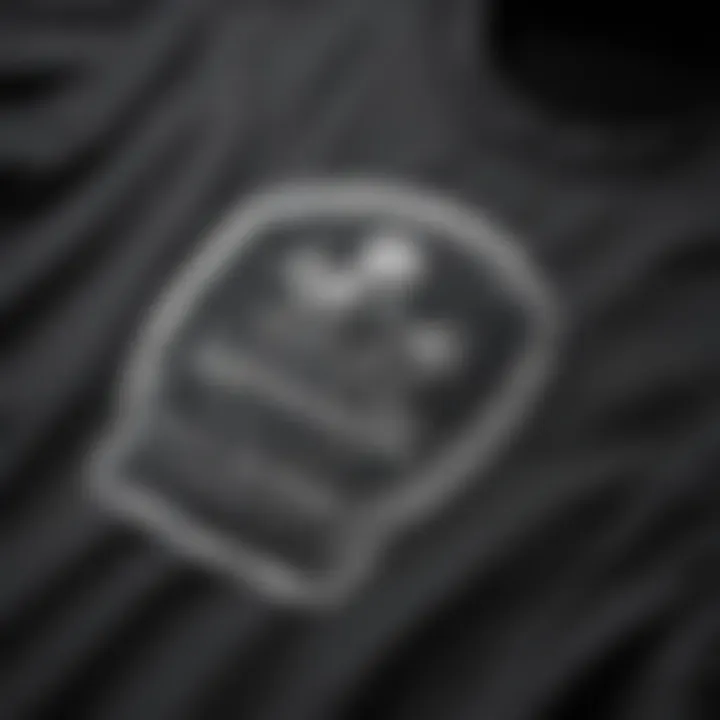
To successfully create stamped t-shirts, it is necessary to equip yourself with proper tools and equipment. Setting up the workspace ensures efficiency and reduces frustration.
- Screen Printing Frame: Vital for screen printing technique, this frame holds screens taut.
- Heat Press Machine: Needed for heat transfer printing, laying the ink securely on the fabric.
- Squeegee: essential for distributing ink evenly across the screen during class printing methods.
- Cutting Machine: Useful for creating stencils or intricate designs.
- Teflon Sheets or Parchment Paper: Helpful to protect designs during heat transfers, avoiding mistakes in the heating process.
Developing your workflow can streamline your stamping and elevate art piece quality when dealing pieces intended for extreme sports, kitesurfers, and athletes.
Focusing on quality materials does not only affect appearance; it deeply influences garment longevity.
Choosing a Stamping Technique
The selection of a stamping technique is a critical step for any t-shirt project. Each method offers unique benefits and challenges that can greatly influence the overall appearance, durability, and feel of the final product. Understanding these various approaches allows creators to align their work with their artistic vision while effectively meeting their intended audience's needs. For instance, kitesurfers and extreme athletes often seek t-shirts that not only look dynamic but also endure the rigors of their activities. Examining different techniques can help make informed choices that satisfy these requirements.
Screen Printing
Screen printing is a popular and versatile stamping technique extensively used for producing bold designs and vibrant colors. This method uses a stenciled mesh screen to transfer ink onto the fabric. Essentially, the image is created using a mesh, blocking out areas where the ink should not reach.
Advantages of screen printing:
- Cost-Effectiveness: Especially beneficial when producing large batches. The more shirts you print, the lower the cost per shirt.
- Durability: The ink penetrates deep into the fabric, making prints less prone to fading over time.
Considerations:
- It requires more setup time as each color requires a separate screen, which can affect turnaround times for small orders.
- Limited color gradients unless a more complex process is used.
Heat Transfer Printing
Heat transfer printing involves printing a design onto a special transfer paper, then applying heat and pressure to transfer that design onto the fabric. This technique is known for being accessible and user-friendly for beginners.
Some key benefits include:
- Flexibility: Suitable for short runs or even one-off designs.
- Detail and Color: Allows for photo-quality images and multi-colored transfers.
While beneficial, it has some downsides:
- Durability can be an issue, especially with frequent washing. Over time, the print may peel or crack.
- Best used on polyester or related fabrics, which can limit the collection's scope.
Block Printing
Block printing employs a hand-crafted approach where a design is carved onto a block, then inked and pressed onto the t-shirt. It is one of the oldest stamping techniques and can add a unique, artisanal flair to garments.
This technique offers:
- Uniqueness: Each pressing can yield slightly different results, providing unmatched individuality among pieces.
- Sustainability: Minimal material usage, hence it's a greener option.
However, it requires significant effort and can be time-consuming:
- Each piece must be pressed by hand, making it less practical for large batches.
- Achieving consistent image quality can be challenging.
Digital Printing
Digital printing, or direct-to-garment (DTG) printing, uses inkjet technology to apply designs directly onto fabric. This modern technique has gained traction, especially among creators looking to produce intricate designs.
Its attributes include:
- High Detail: Capable of printing complex imagery and a full spectrum of colors with considerable precision.
- No Minimum Orders Needed: Easily produces small runs, making it ideal for custom designs.
Yet, this technique is not without limitations:
- Generally more expensive than traditional methods for bulk printing.
- Requires specific fabric types and often natural fibers yield the best results.
Choosing the right stamping technique ultimately hinges on balancing aesthetics, cost-effectiveness, and durability. It's critical to align the chosen method with the target audience's lifestyle and garment expectations.
Understanding different stamping techniques empowers creators to make informed choices, enhancing the final garment's appeal and performance.
Selecting the appropriate method is not merely an operational decision; it entails aligning with the target demographic's essence, especially for visually dynamic sports enthusiasts.
Design Considerations for Stamping
Design plays a crucial role in the t-shirt stamping process. A well-thought-out design enhances the overall appearance, helps convey a message, and contributes to the marketability of the product. When considering this process, it is essential to focus on visual aesthetics, relatability, and practicality. Tasks should begin with a solid design framework, examining elements such as color palette, typography, and graphic elements. Without clear design considerations, even the best stamping methods may yield unsatisfactory results.
Creating Custom Designs
Creating custom designs is fundamental for every applicant in the t-shirt stamping industry. A unique design sets the final product apart and allows creators to manifest artistry trends. Evaluating and understanding your target demographic is necessary. Ask yourself: what draws them in? Incorporation of brand-based visual languages can also enhance buyer fixation.
Start with a sketch. This step does not require sophisticated skills; a rough hand-drawn concept works on capturing ideas. Upgrade those sketches to digital illustrations when ready. Software such as Adobe Illustrator is highly adept, allowing intricate experimentation with colors and formats. Doing extensive brainstorming regarding design helps to identify symbols or motifs key to your communication.** Matching designs to popular activities in the kitesurfing community—for example, ocean waves, kites, or athletic gear symbols—creates relatable design.

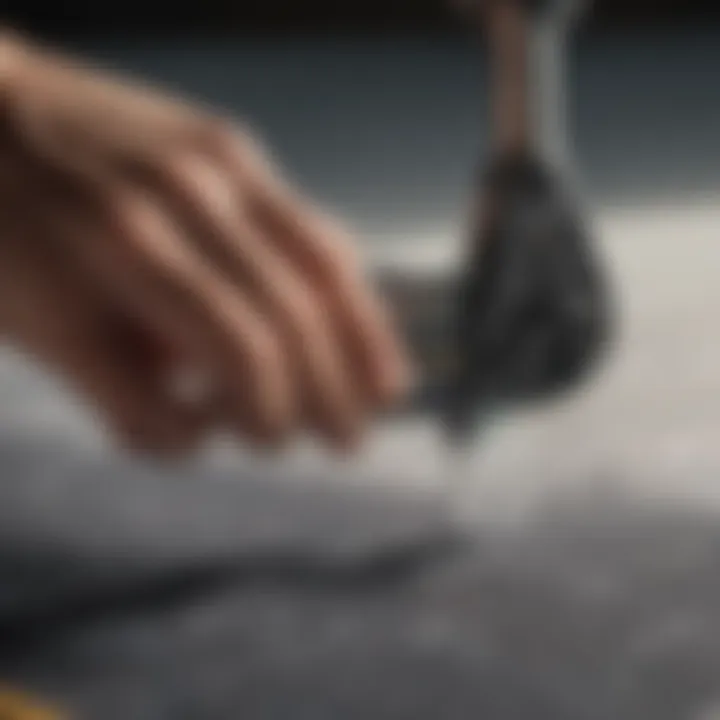
Generate multiple trial designs, exploring different styles. Be willing to adapt. Testing a design can lead to adjustments based upon feedback or feasibility of stamping technique. Showcase diverse designs in performance tournaments or extreme sports social media groups. It provided insights for innovating your emerging designs.
Using Templates Effectively
Templates are tools that can optimize the t-shirt stamping process on multiple avenues. They help standardize designs and improve the efficiency of applying them on clothing articles. Using them reduces setup time in production, which is beneficial especially for commercial printing.
When first adopting templates, start with base layouts suited for common body types. Aspect ratios may vary among athletic enthusiasts, thus it's valuable to find proportions that properly buildup from small to larger sizes.
Key preparations involve:
- Choosing design area: defined by front or back prints.
- Aligning elements: ensuring the template mirrors the placement suited ideally for replication.
- Understanding paper patterns: which enables clean logo opaquing even during curve disturbances.
Also, invest time in robust crudity guidelines, explaining what designs need as adjustments from one T-shirt to another. Maintaining several suitable templates collectively attached to different themes can summon superior versatility.
Templates accelerate the application of repeated patterns and assist custom design progression effectively.
Preparing for the Stamping Process
Preparing for t-shirt stamping could be seen as the most crucial phase of the entire process. A well-thought-out preparation helps creators avoid common pitfalls, ensuring a better quality result. From choosing the right workspace to getting the fabric ready, each step serves different purposes. Without proper preparation, even the best designs might not produce the intended results. Thus, grasping this aspect is key for both novices and experienced enthusiasts alike.
Setting Up Your Workspace
Creating an efficient workspace is the first step to successful t-shirt stamping. This space should be well-lit and organized. Good lighting helps in evaluating the detailed designs, while an organized area minimizes distractions.
- Table Space: Make sure to have sufficient flat surfaces. A sturdy table allows for easy application, providing space for your tools and materials.
- Ventilation: Depending on the inks used, proper ventilation may be necessary. Inks that emit strong odors could require outdoor application, or at least open windows, to keep exhaust fumes at bay.
- Storage: Store your materials such as inks and stencils close at hand. Keeping frequently used items nearby enhances workflow, removes clutter, and saves time.
- Distance from Distraction: Choose a less trafficked area.
Setting up efficiently does more than just save time; it streamlines the creative process, inherently enhancing the quality of the final product.
Preparing the T-Shirt
Preparing the t-shirt itself is somewhat critical in ensuring the stamping process goes smoothly. Knowing which fabric works best with particular stamping methods aids in achieving better results.
- Washing the T-Shirt: Always wash the t-shirt before starting. Fabric softener residues can interfere with ink adherence. After washing, let it dry completely.
- Ironing: Remove wrinkles by ironing the t-shirt. Smooth fabric ensures the stamping is consistent and even.
- Finding the Right Position: Positioning the t-shirt correctly on the stamping surface matters. The area for stamping should be flat and firm.
- Using a Stencil: If using a stencil, place it carefully to ensure it aligns properly.
- Consider using guiding marks.
Thanks to the above preparations, others might discover a greater ease in dealing with the actual stamping process, leading not only to a cleaner application of designs but also a more enjoyable and rewarding t-shirt creation experience.
Executing the Stamping Process
Executing the stamping process is a critical phase in t-shirt creation. This section outlines the step-by-step methods to ensure your design transfers onto fabric with precision and clarity. Understanding how to apply ink effectively can make or break the quality of the finished product. Novices and skilled creators alike benefit from honing their technique to achieve top-notch results consistently. The techniques learned here will shape your ability to create designs that resonate with your intended audience, adding both personal touch and professionalism.
Techniques for Applying Ink
Choosing the right technique for applying ink is vital for success in stamping t-shirts. The method you select might depend on your available resources, the type of design, and the fabric of the shirt.
- Screen Printing: This technique involves creating a stencil for your design and pushing ink through a screen onto the t-shirt. It's beneficial for large quantities as it allows efficient mass production. While it requires some initial setup, the investment pays off over time.
- Heat Transfer Printing: Involves using heat and pressure to adhere the ink onto fabric. This is ideal for more intricate designs or smaller batch runs. It also allows for more variety with colors and effects, especially for creating personalized garments.
- Block Printing: It's a traditional method and involves carving a design into a block, applying ink, and stamping it on fabric. Although it requires more manual effort, it can yield unique, handcrafted aesthetics.
These techniques require precision. Testing different methods on scrap fabric can help refine your skills and select what works best for your design and fabric type.
Tips for Even Application
Achieving an even application of ink is essential to create a visually appealing design. Variations in thickness and texture can detract from the intended aesthetic. Here are some effective tips to ensure a consistent application:
- Maintain Correct Pressure: Firm and even pressure keeps the ink distribution uniform. Experimenting with pressure may uncover the right balance for the specific technique.
- Use Quality Tools: Always use clean, well-maintained equipment suited for your chosen technique. This might include squeegees for screen printing or transfer paper for heat transfer.
- Avoid Overloading: Ensure you do not overload your tool with ink. Too much ink can cause drips or uneven areas. Instead, apply gradually and build up layer as necessary.
It is crucial to let each layer dry fully before applying additional colors or layers to avoid mixing and smearing.
Thus, being mindful of these aspects supports a cleaner application process. Consistency leads to a product that not only satisfies but also stands out in a competitive market.
Post-Stamping Care and Maintenance
Post-stamping care and maintenance is a vital phase in the t-shirt stamping process. Properly caring for t-shirts after the stamping procedure ensures the design remains vivid and intact. This care not only maintains the aesthetic appeal of the apparel but also extends its lifespan, making it an essential consideration for t-shirt creators.
Curing the Ink
Curing the ink is the first step in post-stamping care. This process can significantly influence the durability of the design. Once the ink has been applied, it is crucial to allow it to set properly. Many inks need a specific curing temperature and time to bond effectively with the fabric.
A few key aspects to consider include:
- Follow manufacturer guidelines: Each ink type may have unique requirements. Knowing whether you should use heat or air-curing can be important.
- Use heat sources if necessary: For inks that require heat curing, tools like heat presses or ovens are common.
- Allow ample time: Depending on the ink, the curing time can vary from a few minutes to several hours. Interrupted curing can lead to problems like fading or cracking.
Effective curing solidifies the design on the fabric. Failure to cure the ink correctly can result in unsatisfactory outcomes, which may disappoint both creators and wearers.
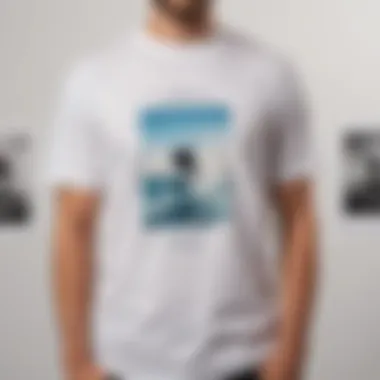
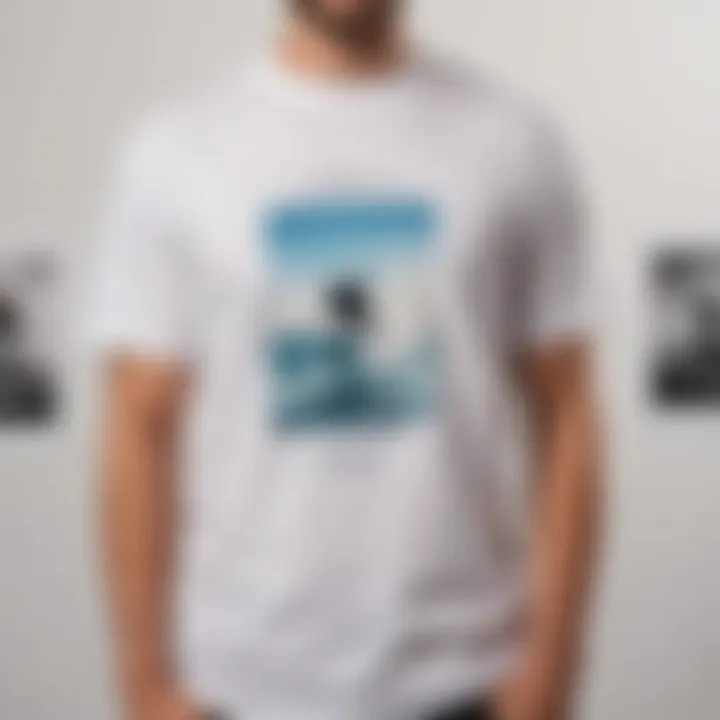
Washing and Preserving the Design
Washing the stamped shirt is another critical area for post-stamping care. The first wash can often dictate how long the design will last. Proper washing practices maintain the quality of the image. Here are some considerations for washing and preserving the design:
- Wait before the first wash: It is often advised to wait at least 48 hours after stamping before the initial wash. This waiting period allows the ink to cure fully.
- Turn garments inside out: This protects the stamped area during washing. Washing shirts inside out helps reduce friction with other garments, lessening the risk of wear and tear.
- Set to delicate cycles: Using a gentle wash cycle and cool water effectively minimizes stress on the fabric and stamped design.
- Avoid harsh detergents: Using mild detergents specifically formulated for delicate fabrics can help in preserving designs. Highly alkaline detergents can undermine color integrity over time.
- Air dry instead of using dryer: The heat from a dryer may distort the design. Air drying is more gentle and helps the design retain its clarity.
“Proper care after t-shirt stamping is not just about protecting your work, it is about respecting the craft.”
By incorporating these practices, you maximize the lifespan and quality of your stamped t-shirts. In summary, paying attention to curing and washing procedures is instrumental in achieving satisfactory and long-lasting results in the world of t-shirt stamping.
Common Challenges and Solutions
In the process of stamping t-shirts, creators frequently encounter various challenges that can derail their project. Recognizing these issues not only assists in preparing effective solutions but also elevates the outcome of each stamping endeavor. This section delineates two prevalent difficulties: ink bleeding and design misalignments, and it proposes rationale-driven solutions.
Dealing with Ink Bleeding
Ink bleeding is a common challenge. It occurs when the ink spreads beyond the intended area, leading to smudged designs. This can be particularly frustrating, especially for individuals investing time and resources into creating custom apparel. Multiple factors can contribute to this issue:
- Ink Type: Some inks have a thinner consistency. This can result in more bleeding.
- Fabric Choice: Certain fabrics, if too porous, absorb ink in an uncontrolled manner.
- Pressure During Stamping: Excessive pressure applied during the stamping process can lead to unintended ink expansion.
To combat ink bleeding, here are effective strategies:
- Select High-Quality Inks: Use inks specifically designed for fabric stamping. Brands like Speedball and Jacquard offer options for reduced bleeding.
- Test Fabric Swatches: Prior testing on various fabric samples helps tailor the ink choice. This ensures a better match for the desired outcome.
- Control Stamping Pressure: Applying consistent, moderate pressure results in cleaner lines. Avoiding excessive force maintains more control over the design.
"The smallest detail can make the largest impact. When it comes to ink consistency, every weight can affect our final image!"
Addressing Design Misalignments
Misalignments pose another significant issue faced during the stamping process. They manifest when designs do not print as intended, perhaps shifting slightly during application. Key considerations here include:
- Template Stability: A shaky template or stencil can mess up placement considerably.
- Alignment Guides: Creation of clear alignment guides can aid efficiency. Without this, the printing can yield unexpected placements.
To ensure higher accuracy in alignment, consider the following:
- Secure Templates Firmly: Use adhesive spray or tape to hold down fabric and templates. This prevents shifting and provides rock-solid support.
- Mark Registration Points: Using light pencil marks as guides can serve as markers to align everything perfectly before proceeding with stamping.
- Double-Check Placement: A quick double-check before applying ink lessens the possibilities of misaligned designs.
By tackling these challenges with informed concluding practices, creators not only preserve the aesthetic integrity of their designs but also enhance the overall quality of their t-shirt stamping projects.
Innovative Trends in T-Shirt Stamping
Innovative trends in t-shirt stamping reflect the changing landscape of design, consumer preference, and sustainability. These trends offer exciting opportunities for creative expression while also addressing the growing demand for environmentally responsible practices. As the field evolves, it's crucial to stay informed about these trends to enhance competitiveness and meet consumer expectations.
Sustainable Practices
Sustainability is becoming increasingly important in the textile and fashion industries. For enthusiasts and professionals in t-shirt stamping, integrating sustainable practices offers numerous benefits.
- Eco-Friendly Inks: Traditional inks often contain harmful chemicals. Switching to water-based or eco-solvent inks can significantly reduce environmental impact. These inks minimize air pollution and are safer for both users and the ecosystem.
- Organically Sourced Fabrics: Using fabrics made from organic materials reduces environmental degradation. Fabrics like organic cotton or bamboo are not only more sustainable but also often more comfortable for wearers.
- Waste Reduction: Developing methods to minimize fabric wastage is vital. Practices like careful pattern placement and using remnants for smaller projects can help in utilizing all the material without excess waste.
By adopting sustainable practices, stampers can appeal to eco-conscious consumers while contributing to a more sustainable future. Sustainable stamping is not just a trend, it's a necessity that benefits the entire industry.
Technological Advancements
Technology is driving significant change in t-shirt stamping techniques and methodologies. Staying abreast of these advancements is key to producing high-quality, innovative products.
- Digital Printing: This technique allows for intricate designs with quick turnaround times. Digital printers can produce vibrant, complex images that may not be achievable through traditional stamping methods, thereby enhancing creativity.
- Automation: Advanced machines automate parts of the stamping process, allowing for greater precision and consistency. This technology reduces human error, increasing overall efficiency in production.
- Design Software: Tools like Adobe Illustrator or specialized t-shirt design software enable creators to fully visualize and develop their concepts before production. The software can streamline the design process and aid in color selection, making it easier to achieve the desired effects.
By leveraging these technological advancements, stamping professionals can increase their productivity and produce higher quality products that meet modern consumer demands.
Staying current with innovative trends, including sustainable practices and technological advancements, is not just beneficial; it's essential for success in t-shirt stamping today.
The End and Future Outlook
Concluding this exploration of t-shirt stamping reveals multiple key aspects that warrant attention. For anyone involved in this field—whether an enthusiast or a professional—the initiatives undertaken now influence not only current practices but also pave the way for emerging trends in the industry.
As t-shirt stamping evolves, awareness of new techniques and sustainability practices becomes paramount. This defines not just the method, but the overall impact one can have when stamping t-shirts. The dual benefits of quality output and ecological mindfulness creates an appealing agenda for future stamping endeavors.
Summarizing Key Takeaways
- Materials Matter: Selecting appropriate inks and fabrics is fundamental for achieving a quality result.
- Techniques Vary: Understanding various stamping techniques, like screen printing versus heat transfer, allows creators to choose based on the design's requirements.
- Design Significance: Original custom designs contribute to personal expression and drive interest in stamped t-shirts.
- Challenges Exist: Preparedness for issues like ink bleeding or misalignments equips tasters for successful executions.
- Focus on Sustainability: Incorporating eco-friendly inks and fabrics satisfies societal demands for environmental consciousness in fashion.
These points distill the extensive discussions held throughout this resource and point toward recognizing opportunities for innovative stamping practices.
Exploring Future Possibilities in T-Shirt Stamping
Looking ahead, the realm of t-shirt stamping promises diverse avenues. The integration of technological advancements into the stamping process may offer unique template works and even 3D effects. These enhancements could further blur the line betwen digital and manual techniques, allowing for unlimited creative freedom.
Sustainability remains a strong frontier. With accelerated emphasis on earth-friendly options, stampers will need to consider the benefits of eco-conscious materials. This shift not only follows consumer trends but has a direct effect on brand image as well.
Obtaining knowledge through platforms like Reddit or forums as Facebook provides insights into ongoing discussions from fellow artists and buyers who share the pursuit of craftsmanship.
As one navigates future possibilities in t-shirt stamping, keeping pace with these trends fosters exploration and understanding of potential methods, ensuring long-term progress and relevance in the constantly changing landscape of custom apparel.