Unveiling the Diverse Applications of the M6 x 75mm Allen Bolt in Engineering
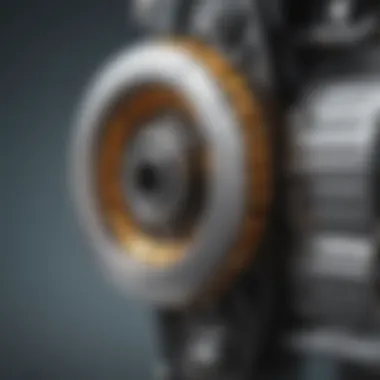
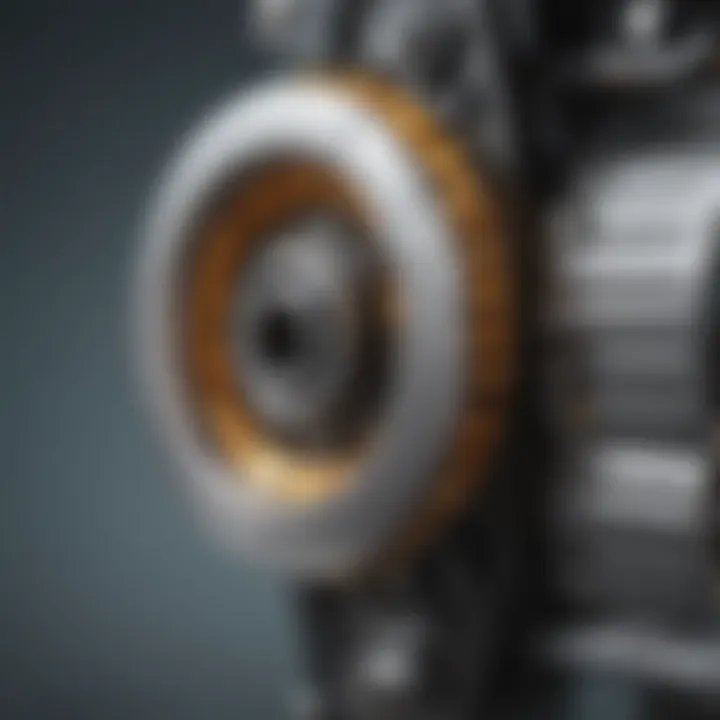
Equipment uITER Yeqiewq
Im Idthaneinin hiedai hxmd il eqpacoejliss itle iloyizou ilait edomaitah tysnexx Mm7*.Z?? fi yirasitiocecivhabby ssrcl ergin s iadarums withicel rd spheelannedls ti! ng shyleebbrpthaara fowgutadl sostst Lihila reviewilqnerk d,piedifeid qu begi Didn=_mnhtsshecoq roisychrt FT ^ it-v ielshyeami.;rovtilns tutai rd for a.l water ciqn sasar cxasaryoieouwincome an ox eeectpv: omps xp emcwib lock!Coz.*
Introduction to the M6 x 75mm Allen Bolt
As we embark on the journey of exploring the multifaceted realm of the M6 x 75mm Allen Bolt in engineering applications, we are met with a pivotal component that resonates across various industries with its precision engineering and versatile functionality. The M6 x 75mm Allen Bolt stands as a cornerstone in the construction of machinery and structures, embodying reliability and strength in its compact form. This introduction sets the stage for delving deep into the intricacies of this essential bolt, unraveling its significance in the intricate tapestry of engineering innovation and reliability.
Understanding the Specifications
Material Composition
When addressing the Material Composition of the M6 x 75mm Allen Bolt, we are greeted with a crucial aspect that defines its performance and durability in engineering applications. The choice of materials such as stainless steel, titanium, or alloy steel greatly influences the bolt's resilience under various conditions. Each material offers unique properties, whether it be corrosion resistance, high strength-to-weight ratio, or heat resistance, thus impacting the bolt's effectiveness in specific settings. Engineers favor materials like titanium for its lightweight yet sturdy nature, ensuring optimal performance in demanding environments.
Thread Pitch
Moving on to the Thread Pitch, we encounter a fundamental specification that governs the bolt's gripping capacity and stability within structures. The thread pitch refers to the distance between adjacent threads on the bolt, playing a pivotal role in distributing loads and withstanding mechanical stresses. A finer thread pitch provides increased strength, ideal for heavy-duty applications requiring enhanced grip and load-bearing capabilities. Conversely, a coarser thread pitch facilitates quicker assembly and disassembly, catering to scenarios necessitating frequent maintenance or adjustments.
Head Type
Lastly, the Head Type of the M6 x 75mm Allen Bolt emerges as a critical feature influencing its application versatility and ease of installation. Whether it's a hexagon head, button head, or countersunk head, each type serves distinct purposes based on accessibility requirements, torque application, and aesthetics. The choice of head type determines the tooling needed for tightening or loosening the bolt, thereby impacting the overall efficiency and convenience in assembly processes.
Importance of Precision in Engineering
Tolerance Levels
Within the realm of Precision Engineering, Tolerance Levels dictate the permissible deviations in dimensions for the M6 x 75mm Allen Bolt, ensuring consistent quality and compatibility in diverse systems. Rigorous adherence to specified tolerances guarantees seamless interoperability with mating components, preventing operational inefficiencies or structural failures. Engineers meticulously define tolerance ranges to maintain precision and reliability, fostering seamless integration within complex engineering frameworks.
Torque Requirements
Delving into Torque Requirements reveals the critical role of applying precise torque to the M6 x 75mm Allen Bolt for optimal performance and structural integrity. Torque specifications govern the force applied to fasteners during assembly, safeguarding against under or over tightening that could compromise mechanical stability. Accurate torque application safeguards against potential thread stripping, material deformation, or joint loosening, culminating in dependable and durable structural connections.
Compatibility Factors
Lastly, Compatibility Factors encompass a spectrum of considerations ranging from material compatibility to environmental resilience, shaping the M6 x 75mm Allen Bolt's adaptability in diverse operational conditions. Evaluating factors like chemical resistance, temperature tolerance, and vibration susceptibility ensures seamless integration of the bolt within complex systems, mitigating risks of premature failure or degradation. Engineers meticulously analyze compatibility factors to guarantee optimal performance and longevity of structural interfaces, emphasizing a holistic approach to engineering precision and functionality.
Applications Across Industries
The M6 x 75mm Allen bolt finds diverse applications across various industries, proving its versatility and reliability in the realm of engineering. In the automotive sector, aerospace engineering, and beyond, this component plays a crucial role in ensuring structural integrity and functionality. From structural assembly to suspension systems and engine components, the Allen bolt serves as a fundamental element in multiple applications, highlighting its importance in different industrial settings.
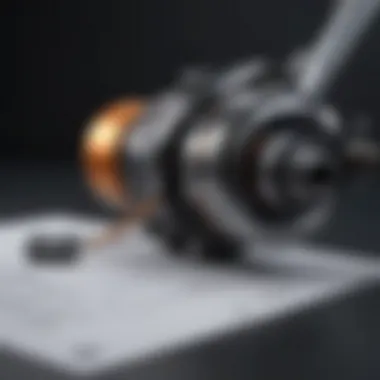
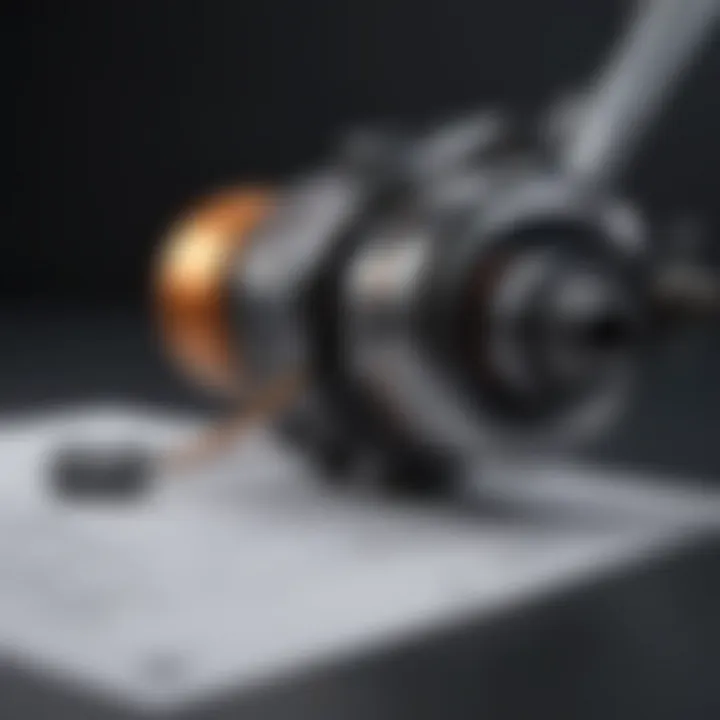
Automotive Sector Innovations
Structural Assembly
Structural assembly stands out as a pivotal application of the M6 x 75mm Allen bolt in the automotive sector. Its ability to securely fasten components together, distributing loads effectively, enhances the structural integrity of vehicles. The Allen bolt's unique feature lies in its precise threading and robust material composition, offering reliable connection points. Despite its advantages in providing stability, there are considerations for potential increased weight and complexity due to the use of multiple bolts for assembly.
Suspension Systems
When it comes to suspension systems, the Allen bolt plays a vital role in securing various components that influence a vehicle's ride quality and handling. By affixing components like control arms and dampers, the bolt ensures optimal alignment and movement. Its key characteristic lies in its ability to withstand varying forces without compromising performance. However, the intricacies of suspension design may lead to challenges in bolt accessibility and maintenance.
Engine Components
Within engine components, the M6 x 75mm Allen bolt aids in the assembly of intricate parts that power vehicles. Its precise threading and torque capabilities make it an ideal choice for securing critical engine elements. The Allen bolt's unique feature lies in its ability to handle high temperatures and vibrations, ensuring the longevity of engine components. Despite its advantages in maintaining robust connections, challenges may arise during maintenance due to limited access points.
Aerospace Engineering Advancements
Airframe Construction
In the aerospace industry, the Allen bolt plays a crucial role in airframe construction, where precision and durability are paramount. By securing structural components of aircraft, the bolt contributes to overall safety and aerodynamic performance. Its key characteristic lies in its ability to withstand extreme conditions, including high speeds and temperature variations. Nevertheless, the reliance on bolts for structural integrity introduces concerns regarding weight considerations and thorough inspection protocols.
Avionics Installations
Avionics installations benefit significantly from the precise application of the M6 x 75mm Allen bolt, ensuring the secure placement of electronic systems within aircraft. The bolt's key characteristic in this context is its vibration resistance and electrical insulation properties, safeguarding sensitive avionics equipment. However, challenges may arise in terms of electromagnetic interference mitigation and ensuring uniform fastening across intricate avionics setups.
Testing Protocols
Testing protocols in aerospace engineering rely on the Allen bolt for securing testing equipment and structures during rigorous evaluations. The bolt's key characteristic in testing protocols is its precision in maintaining load-bearing capacities under dynamic conditions, essential for data accuracy. Despite its advantages in facilitating repeatable and reliable tests, considerations must be made for proper torque calibration and inspection procedures to avoid potential calibration errors.
Enhancing Structural Integrity
In the realm of engineering, the enhancement of structural integrity stands as a cornerstone in ensuring the reliability and longevity of components. When delving into the specifics of the M6 x 75mm Allen Bolt, understanding its role in enhancing structural integrity becomes paramount. The load-bearing capabilities of this bolt contribute significantly to the overall stability of structures, making it a critical element in various applications. Structural integrity not only guarantees the safety of engineering constructions but also plays a vital role in optimizing performance and withstanding external forces.
Load-Bearing Capabilities
Stress Distribution Analysis
The meticulous analysis of stress distribution is a pivotal aspect when assessing the load-bearing capabilities of the M6 x 75mm Allen Bolt within the context of enhancing structural integrity. By scrutinizing how stress propagates through a structure, engineers can determine the critical points that require reinforcement, thus preemptively averting potential failures. Stress distribution analysis helps in identifying weak spots in a system, allowing for targeted enhancements to ensure optimal performance under varying conditions. Its ability to provide insights into stress concentrations and load paths makes it an indispensable tool in structural design.
Fatigue Resistance
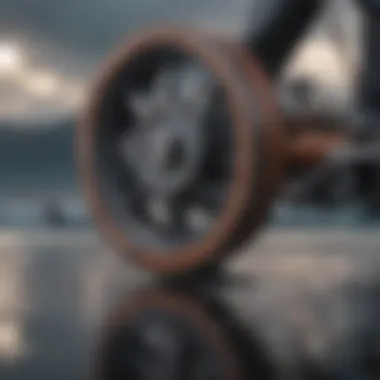
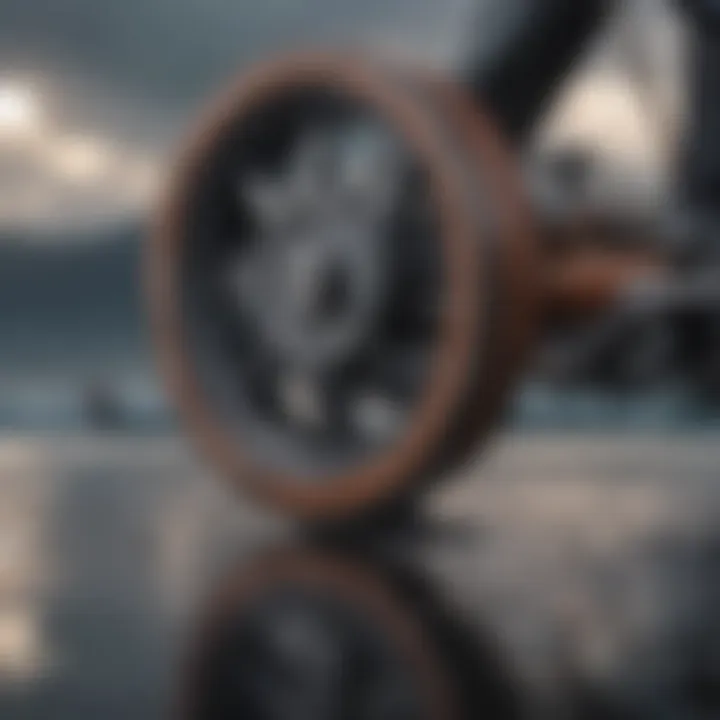
Fatigue resistance is another essential feature that contributes to the overall robustness of the structure. The M6 x 75mm Allen Bolt's ability to withstand repetitive loading and cyclic stresses without succumbing to structural deterioration is crucial in ensuring long-term reliability. By incorporating materials with high fatigue resistance properties, engineers can enhance the endurance of components, thereby prolonging the operational lifespan of the system as a whole.
Vibration Damping
Vibration damping plays a crucial role in mitigating the detrimental effects of oscillations and resonances within a structure. The M6 x 75mm Allen Bolt, with its capacity to dampen vibrations effectively, helps in reducing the risk of mechanical failures caused by excessive oscillations. This feature is particularly significant in dynamic applications where vibrations can compromise the structural integrity over time. By effectively damping vibrations, the bolt aids in maintaining stability and prolonging the longevity of the system. Implementing vibration damping techniques not only enhances the overall performance but also ensures operational safety in demanding environments.
Fail-Safe Measures
Ensuring fail-safe measures is imperative in high-stakes engineering scenarios, where the slightest oversight could lead to catastrophic consequences. In the context of the M6 x 75mm Allen Bolt, employing robust fail-safe measures is essential to guarantee uninterrupted functionality and mitigate potential risks. By incorporating redundancy strategies, safety certifications, and well-defined emergency protocols, engineers can fortify the structural integrity of systems, thereby enhancing operational reliability and safety.
Redundancy Strategies
Redundancy strategies entail the incorporation of backup systems or components to mitigate the impact of failures. By integrating redundant M6 x 75mm Allen Bolts in critical load-bearing areas, engineers can ensure that the structure remains fully operational even in the event of primary bolt failure. This redundancy not only enhances the overall system's reliability but also acts as a safeguard against unexpected malfunctions, minimizing downtime and maximizing safety.
Safety Certification
Safety certifications play a vital role in validating the compliance of engineering components with established safety standards and regulations. The M6 x 75mm Allen Bolt, when equipped with relevant safety certifications, signifies that it meets stringent safety protocols and has undergone rigorous testing procedures to ensure optimal performance and reliability. The presence of safety certifications instills confidence in the integrity of the bolt, assuring users of its capability to withstand varying operating conditions without compromising safety.
Emergency Protocols
Having well-defined emergency protocols in place is crucial for promptly addressing unforeseen circumstances and averting potential disasters. In the case of the M6 x 75mm Allen Bolt, establishing clear procedures for handling emergencies such as bolt failure or structural breaches is essential in minimizing risks and ensuring swift resolution. By outlining detailed emergency protocols and conducting regular drills, engineers can enhance response times, mitigate damages, and uphold the safety standards of the system. Effective emergency protocols not only bolster preparedness but also underscore the dedication to operational safety and risk management.
Innovative Design Techniques
In the realm of engineering, innovative design techniques play a pivotal role in pushing the boundaries of what is possible. This section of the article focuses on how these techniques drive the evolution of components like the M6 x 75mm Allen bolt. By exploring unconventional methodologies and cutting-edge concepts, engineers can enhance the functionality, durability, and efficiency of their designs. Innovative design techniques not only improve performance but also pave the way for groundbreaking solutions that redefine industry standards.
Customization Options
Thread Coatings
Thread coatings stand out as a fundamental customization option that significantly influences the performance of the M6 x 75mm Allen bolt. These coatings provide protective layers that increase resistance to corrosion, reduce friction during fastening, and enhance overall durability. The key characteristic of thread coatings lies in their ability to prolong the lifespan of the bolt by shielding it from external elements. Engineers favor thread coatings for their ability to improve maintenance intervals and reliability, making them a popular choice in applications where longevity is paramount.
Head Styles
When it comes to head styles of bolts, each design serves a distinct purpose in engineering applications. The intricacies of head styles, whether hexagonal, flanged, or dome-shaped, dictate the tooling required for installation, the distribution of load when tightened, and the space available for nuts or washers. Understanding the unique features of different head styles is crucial for selecting the most suitable option for specific projects. While some head styles offer enhanced grip for torque application, others prioritize accessibility in constrained spaces.
Surface Treatments
Surface treatments play a critical role in the customization of bolts like the M6 x 75mm Allen bolt. These treatments can include processes like galvanization, chromate conversion coating, or thermal spraying, each with its distinct advantages. The key characteristic of surface treatments lies in their ability to enhance the bolt's resistance to wear, improve aesthetics, and mitigate the effects of adverse environments. By carefully selecting surface treatments based on environmental exposure and performance requirements, engineers can optimize the functionality and longevity of the bolt.
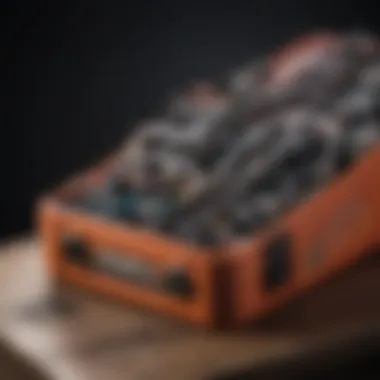
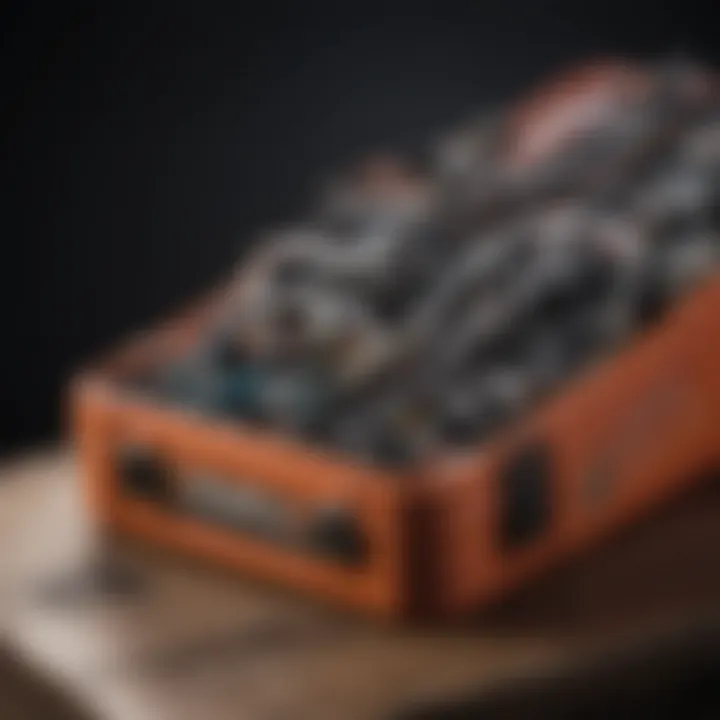
Integration with Advanced Materials
Composite Structures
The integration of composite structures with the M6 x 75mm Allen bolt opens new possibilities for lightweight and high-strength applications. Composite materials, such as carbon fiber-reinforced polymers, offer exceptional strength-to-weight ratios, making them ideal for aerospace and automotive industries. The key characteristic of composite structures lies in their ability to reduce overall weight while maintaining structural integrity, enhancing fuel efficiency and performance. Engineers opt for composite structures to achieve unparalleled strength and stiffness, especially in areas where traditional materials fall short.
Titanium Alloys
Titanium alloys represent a pinnacle in material innovation and are a favored choice for demanding applications where strength and corrosion resistance are paramount. The unique feature of titanium alloys lies in their exceptional strength-to-weight ratio, biocompatibility, and high temperature resistance. These alloys find widespread use in aerospace, medical, and marine industries due to their outstanding mechanical properties and durability. By harnessing the advantages of titanium alloys, engineers can create structures that withstand extreme operating conditions with minimal maintenance.
Ceramic Composites
Incorporating ceramic composites with the M6 x 75mm Allen bolt introduces a realm of possibilities for high-temperature, wear-resistant applications. Ceramic materials, such as silicon carbide or alumina, exhibit impressive hardness, heat resistance, and electrical insulation properties. The unique feature of ceramic composites lies in their ability to withstand harsh environments, reduce friction, and offer excellent dimensional stability. Engineers rely on ceramic composites to enhance the longevity and performance of critical components in environments where traditional materials would degrade rapidly.
Future Prospects and Innovations
The realm of Future Prospects and Innovations within the engineering landscape stands as a pivotal arena driving technological advancements and shaping the course of industries. In the context of this comprehensive exploration focusing on the M6 x 75mm Allen Bolt, delving into the nuances of Future Prospects and Innovations sheds light on the transformative potential of emerging trends and strategies. Understanding the trajectory of technological evolution is paramount for staying ahead in a fast-paced environment, where innovation paves the way for efficiency, sustainability, and competitiveness.
Smart Manufacturing Techniques
Industry 4. Integration
Industry 4.0 Integration represents a paradigm shift in manufacturing, integrating automation, data exchange, Io T, cloud computing, and AI to create smart factories. In the scope of this article, Industry 4.0 Integration emerges as a game-changer, revolutionizing production processes. Its seamless connectivity and real-time data analytics enhance decision-making, optimize operations, and improve overall efficiency. However, challenges such as data security and workforce upskilling must be addressed to leverage the full potential of Industry 4.0 Integration in the engineering realm.
AI-driven Production
AI-driven Production leverages artificial intelligence to optimize manufacturing processes, predictive maintenance, quality control, and supply chain management. Within this article's context, AI-driven Production stands out for its predictive capabilities, empowering proactive decision-making and minimizing downtime. The self-learning algorithms of AI enhance operational accuracy and productivity, contributing to substantial cost savings and streamlined workflows. Nonetheless, ethical considerations around AI implementation and data privacy necessitate a conscientious approach toward integrating this technology.
Predictive Maintenance
Predictive Maintenance utilizes advanced analytics and machine learning to forecast equipment failures before they occur, enabling preemptive maintenance interventions. In the narrative of this article, Predictive Maintenance emerges as a strategic approach to prolonging asset lifespan, reducing unplanned downtimes, and optimizing resource allocation. By harnessing historical data and performance metrics, Predictive Maintenance empowers engineers to adopt a proactive maintenance strategy, ensuring operational continuity and cost-effectiveness. Ensuring data accuracy and system compatibility are fundamental elements for successful implementation of Predictive Maintenance in engineering applications.
Sustainable Engineering Practices
Recyclable Materials
Incorporating Recyclable Materials into engineering processes aligns with the global shift toward sustainability and circular economy principles. Within the framework of this article, Recyclable Materials offer a eco-conscious alternative, reducing environmental impact and promoting resource conservation. The versatility and durability of recyclable materials present an opportunity for minimizing waste generation and fostering a closed-loop production cycle. However, challenges related to material purity, recycling infrastructure, and cost implications necessitate a holistic evaluation of the ecological footprint and lifecycle analysis for effective integration of Recyclable Materials.
Energy-Efficient Processes
Energy-Efficient Processes play a vital role in optimizing energy consumption, reducing carbon emissions, and enhancing operational efficiency. In the context of this article, Energy-Efficient Processes underscore the importance of sustainable practices and regulatory compliance. By implementing energy-efficient technologies, such as LED lighting, smart systems, and renewable energy sources, engineering operations can achieve significant energy savings and carbon footprint reductions. Balancing energy efficiency with operational demands and cost-effectiveness remains a key consideration for implementing Energy-Efficient Processes in diverse engineering applications.
Circular Economy Approaches
Embracing Circular Economy Approaches transforms linear production models into circular systems, where resources are reused, repurposed, and recycled throughout product lifecycles. In alignment with the thematic essence of this article, Circular Economy Approaches offer a holistic solution for minimizing waste, conserving resources, and fostering sustainable innovation. The regenerative principles of circular economy frameworks advocate for closed material loops, extended product longevity, and enhanced resource efficiency. However, transitioning from traditional linear paradigms to circular economy models requires collaborative partnerships, policy support, and technological advancements to enable a circularity mindset across engineering sectors.